We gebruiken cookies om u de beste ervaring op onze website te bieden. Door op 'Accepteren' te klikken, stemt u in met ons gebruik van cookies.
#
Machinemax
MachineMax optimaliseert Shell Raffinaderij
Het Shell Sarnia Manufacturing Centre is een chemische fabriek in Sarnia...
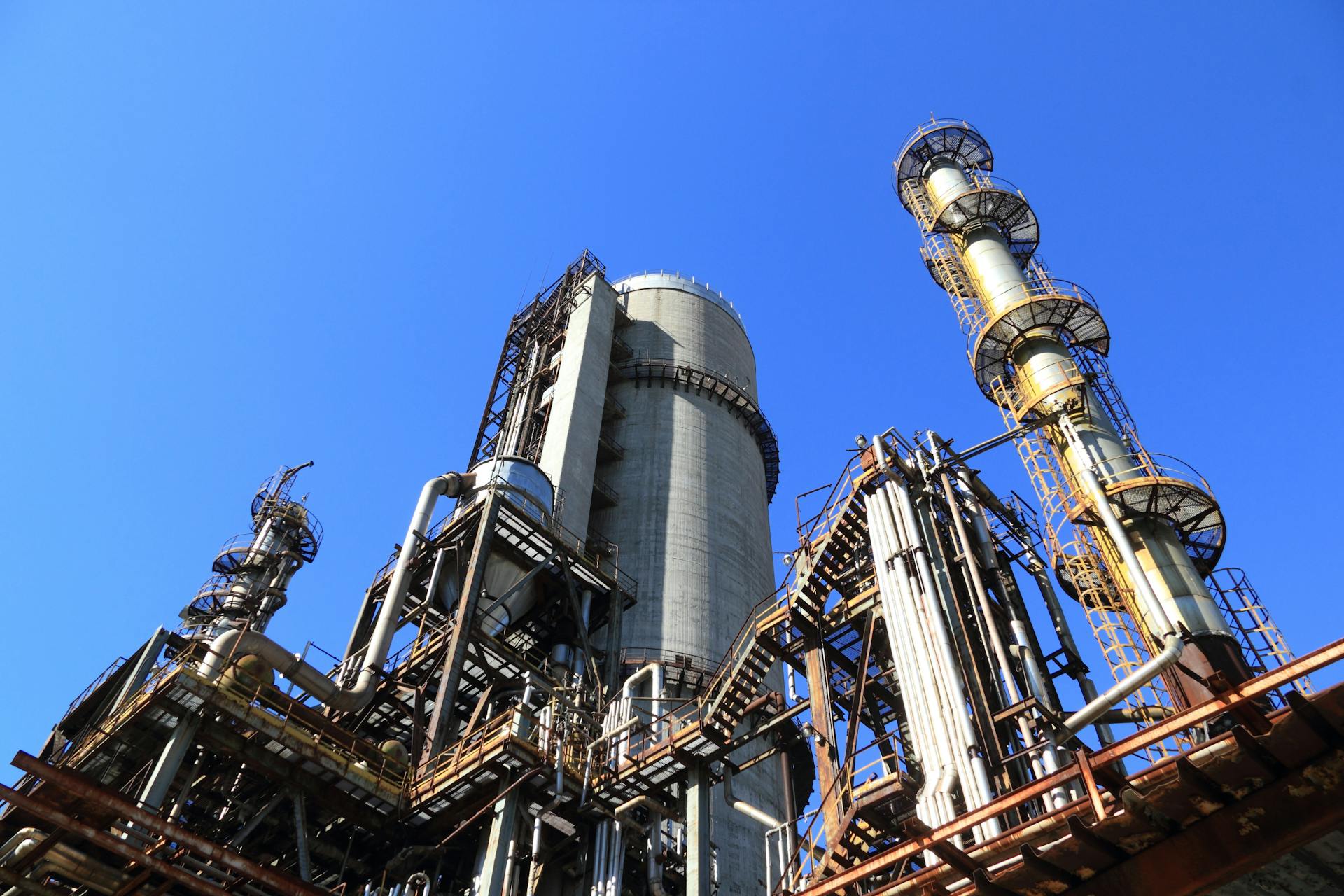
Inleiding
Het Shell Sarnia Manufacturing Centre is een chemische fabriek in Sarnia, Ontario, Canada. Het produceert een scala aan producten, waaronder brandstoffen, smeermiddelen en petrochemicaliën, en wordt geëxploiteerd door Shell Canada Limited, een dochteronderneming van Shell plc.
Het Sarnia Manufacturing Centre is een belangrijk onderdeel van de geïntegreerde chemische activiteiten van Shell en is de thuisbasis van een aantal onderzoeks- en ontwikkelingsprojecten die gericht zijn op het verbeteren van de efficiëntie en duurzaamheid van chemische productieprocessen en duurzaamheid van chemische productieprocessen.
Uitdagingen
Het Sarnia Manufacturing Centre heeft een aanzienlijk aantal aannemers die elk jaar op het terrein werken en meer dan 100 machines op het 540 hectare grote terrein. De belangrijkste uitdaging voor de raffinaderij waseen gebrek aan inzicht in de manieren waarop de machines werden gebruikt en de impact die dit had op de activiteiten van de faciliteit.
Het team van Shell Sarnia had geen inzicht in waar de machines zich bevonden, hoe ze werden gebruikt, wat de CO2-impact was en hoeveel uur er werd gewerkt, of de gewerkte uren. Dit gebrek aan gegevens maakte het voor de raffinaderij moeilijk om haar activiteiten te stroomlijnen en verbeter mogelijkheden te identificeren en mogelijkheden voor verbetering te identificeren.
Oplossing
Om deze uitdagingen het hoofd te bieden, besloot Shell Sarnia het MachineMax-systeem uit te proberen. In eerste instantie sloot het team vier machines op het systeem aan om te zien wat het voor hun werkzaamheden kon betekenen. Toen ze de gegevens van deze vier machines ontvingen, waren ze verbaasd dat geen van de machines aan hun verwachtingen voldeed. Dit leidde ertoe dat het team het MachineMax systeem uitbreidde over het gehele terrein van 540 hectare doormeer dan 100 machines aan te sluiten.
Resultaten
De implementatie van het MachineMax systeem bracht een ongelooflijk inzicht in de mogelijkheden voor verbetering in het Sarnia Manufacturing Centre. Door de gegevens van het systeem te analyseren, was het team van Shell Sarnia in staat om een aantal inefficiënties in hun activiteiten te identificeren, waaronder het feit dat het gebruik van een aantal van hun machines onder één uur per maand lag. Dit leidde tot het besluit om de eerste vijf voertuigen helemaal uit het wagenpark te verwijderen en andere Shell-voertuigen op andere locaties in te zetten om de werkzaamheden te stroomlijnen en de onderhoudskosten te verlagen.
Toen Jason werd gevraagd naar de impact die dit had op het hele bedrijf, zei hij:
"Door de eerste vijf voertuigen uit het wagenpark te halen en ongeveer tien andere opnieuw in te zetten, heeft het MachineMax platform zichzelf al terugverdiend voor de komende vijfjaar, en het is nog maar vier maanden geleden"
Naast het identificeren van inefficiënties hielp het MachineMax systeem het team van Shell Sarnia ook om het stationair draaien op locatie te verminderen door inzicht te geven in de hoeveelheid stationair draaien die plaats vond. Dit leidde tot de implementatie van toolbox gesprekken voor operators en het gebruik van gegevensvan MachineMax om goede werkmethodes te prijzen en gebieden voor verbetering te identificeren.
Conclusie
het Shell Sarnia Manufacturing Centre aanzienlijke voordelen opgeleverd voor de activiteiten van de faciliteit. Door real-time tracking en analyses voor zware machines te bieden, heeft het systeem het team van Shell Sarnia geholpen hun activiteiten te stroomlijnen, inefficiënties te identificeren en stationair draaien op locatie te verminderen. Het resultaat is dat de raffinaderij de efficiëntie en duurzaamheid van haar activiteiten heeft kunnen verbeteren en zich in een goede positie bevindt om in de toekomst op deze successen voort te bouwen.
Jason verklaarde dat:
"Dit is nog steeds een proces, we proberen vele jaren van inefficiënt gedrag uit te wissen en dit is niet de schuld van de operator, maar het zal een voortdurende follow-up vergen en we hebben nu tenminste volledig zicht op de situatie, de vooruitgang en we kunnen de verandering en de impact daadwerkelijk meten."
Jouw processen optimaliseren?
Ontdek hoe je processen eenvoudig kunt verbeteren voor betere resultaten met monytr.
Maak een afspraak
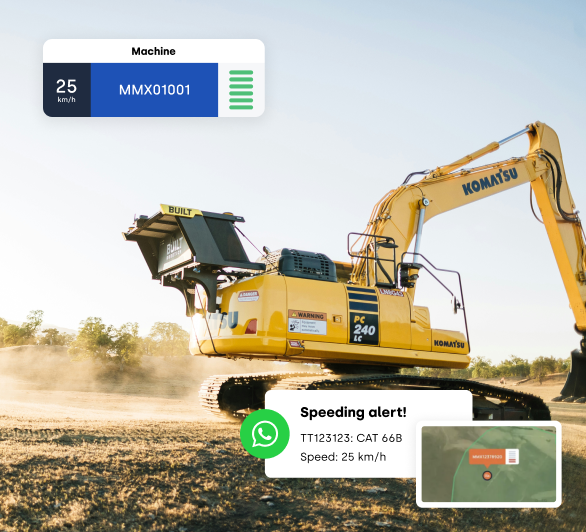